全切削から冷間鍛造+切削加工への工法転換によるコストダウン事例
課題
原価低減の課題
導入効果
コストダウン
業界
自動車業界
用途
オイルポンプ用のリリーフバルブ
BEFORE
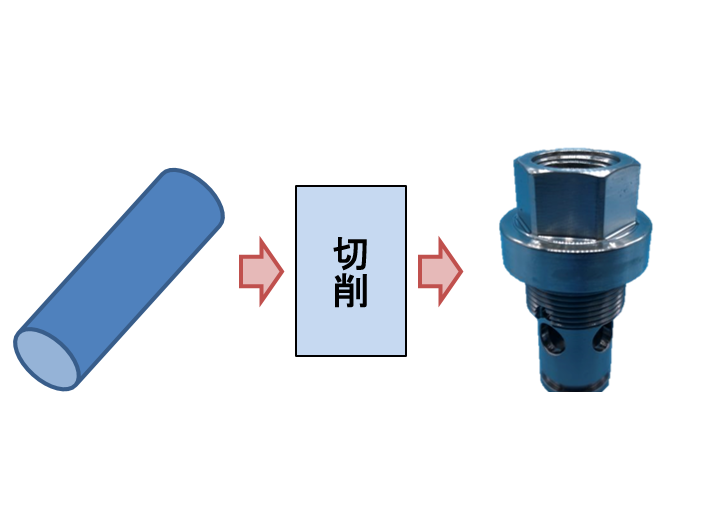
この事例は、オイルポンプ用のリリーフバルブについてコストダウンができないか?ということでご相談をいただいた事例です。
従来は、S45Cのバー材を素材として、切削加工により仕上げていましたが、コストダウンのために他工法での加工を検討することにしました。
従来は、S45Cのバー材を素材として、切削加工により仕上げていましたが、コストダウンのために他工法での加工を検討することにしました。
AFTER
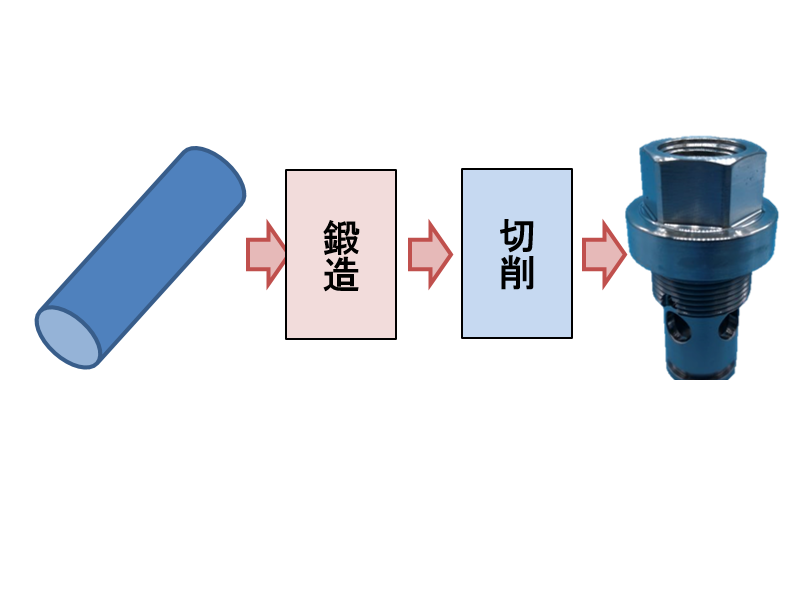
そこで、精密バルブ パーツ・継手 組立/製造センターでは冷間圧造による工法転換・コストダウンをご提案しました。
まず、冷間圧造に切り替え、材質をS15Cに変更し、材料費のコストダウンを行い、6角(2面巾26mm)部を成形しました。
細かな箇所は切削加工を行うことで仕上げていますが、材質変更と切削工程の工数の見直しにより、1個当たり10円のコストダウンに成功しました。
まず、冷間圧造に切り替え、材質をS15Cに変更し、材料費のコストダウンを行い、6角(2面巾26mm)部を成形しました。
細かな箇所は切削加工を行うことで仕上げていますが、材質変更と切削工程の工数の見直しにより、1個当たり10円のコストダウンに成功しました。
ポイント
精密バルブ パーツ・継手 組立/製造センターでは、材料変更や、工法転換によるコストダウン提案を得意としています。
こちらの事例では、全切削で加工を行っていた所から、冷間鍛造+切削加工により製品を仕上げています。
結果として、材料コストの削減と工程集約によるコストダウンを実現しました。
量産パーツのコストダウンでお困りの方は精密バルブ パーツ・継手 組立/製造センターにお問い合わせください。