パイプ形状の3次元成形の冷間圧造化によるコストダウン
課題
材料費・工数削減
導入効果
コストダウン
業界
自動車業界
用途
オイルジェット用のパイプノズル
BEFORE
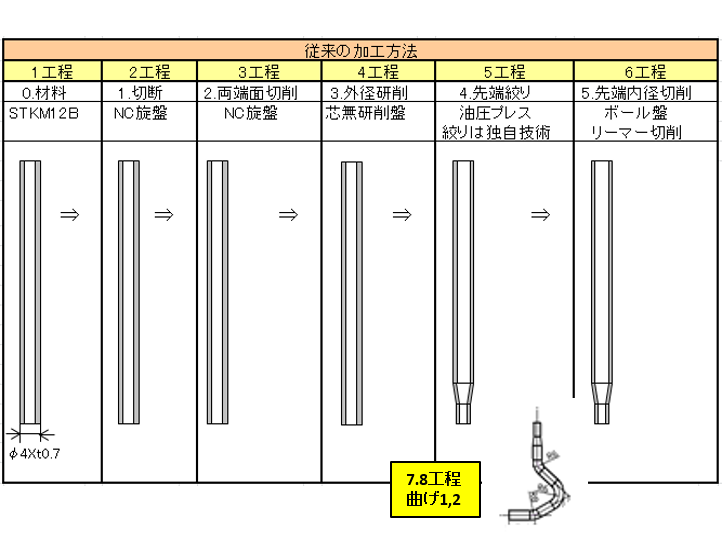
この事例は、3次元的な複雑形状をもつパイプ部品について、コストダウンを検討した事例です。従来の部品製作の工程は、下記の通りです。
①パイプ鋼材を購入
②切断
③両端面切削
④外径研削
⑤先端絞り
⑥先端内径切削
をしていました。
しかし、
①購入パイプが高価であること
②パイプへの追加工で加工工程有り(外注)
そのため、社内の付加価値が低く、購入品・外注費のためにコストダウンを実現することができませんでした。
①パイプ鋼材を購入
②切断
③両端面切削
④外径研削
⑤先端絞り
⑥先端内径切削
をしていました。
しかし、
①購入パイプが高価であること
②パイプへの追加工で加工工程有り(外注)
そのため、社内の付加価値が低く、購入品・外注費のためにコストダウンを実現することができませんでした。
AFTER
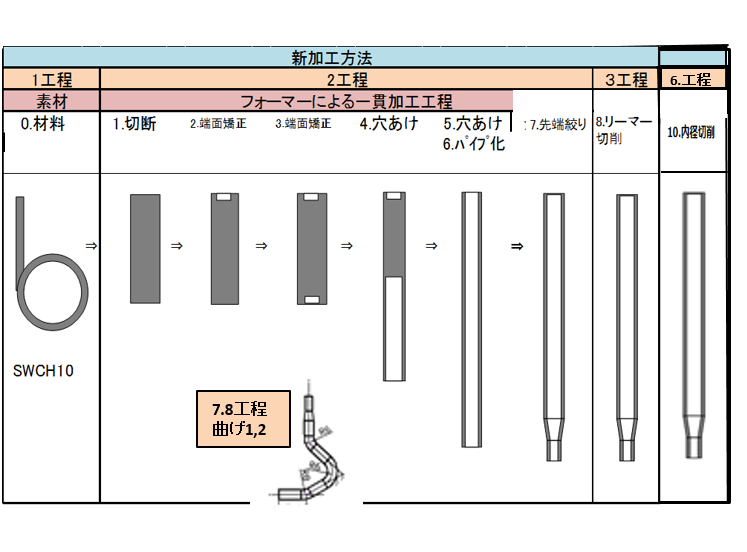
そこで、精密バルブ パーツ・継手 組立/製造センターでは、コストを抑えることを念頭に、工法転換のご提案をいたしました。
具体的には以下の様に、コイル材を購入、切断からパイプ化までを冷間圧造化し、工程集約を行いました。
①コイル材を購入
②切断・端面矯正・穴あけ・パイプ化までを冷間圧造化
③熱処理
④外径研磨
⑤先端絞り
⑥内径切削
結果として、冷間圧造によるパイプ成形を行うことで、パイプを購入する場合と比較して材料のコストダウンと外注比率削減によるコストダウンに成功しました。
具体的には以下の様に、コイル材を購入、切断からパイプ化までを冷間圧造化し、工程集約を行いました。
①コイル材を購入
②切断・端面矯正・穴あけ・パイプ化までを冷間圧造化
③熱処理
④外径研磨
⑤先端絞り
⑥内径切削
結果として、冷間圧造によるパイプ成形を行うことで、パイプを購入する場合と比較して材料のコストダウンと外注比率削減によるコストダウンに成功しました。
ポイント
このように、精密バルブ パーツ・継手 組立/製造センターでは、冷間圧造への工法転換によるコストダウンを提案することが可能です。
他社では難しいとされる絞りを伴うような冷間圧造も得意としており、パイプを購入する場合と比較しても圧倒的なコストメリットの提供が可能です。
全切削で行っている製品の冷間圧造化によるコストメリットを知りたいという方は、当社にお問い合わせください。
他社で作れないと断られてしまった製品でも、精密バルブ パーツ・継手 組立/製造センターが解決いたします!