冷間鍛造とは、素材に高圧をかけて金型に素材を押し付けることで塑性変形を行わせる工法を指します。本ページでは、冷間鍛造を用いてステンレス素材を塑性変形させる場合の加工における難しさや、製品の特性などをご紹介いたします。
ステンレス材は、一般的に硬度が高く、加えて耐食性などを持つ素材として扱われており、冷間鍛造で塑性変形を行うことで、内部組成・構造が変化し、引張強度や硬度が向上するとともに表面は金型の圧力により綺麗な仕上がりが期待できます。
一方で、常温かつ高圧力により塑性変形を行う冷間鍛造では、変形の過程でステンレスの硬度が高くなるため、加工性が悪くなっていくとも言われています。
当社ではステンレス材への冷間鍛造により、他社では難しいとされる細穴加工が可能で、さらに切削でしかできないような複雑な形状も冷間鍛造で行うことが可能です。本項では、一般的な情報から当社ならではの加工技術も解説していますので、ぜひご覧ください。
ステンレス製品を全切削から冷間鍛造化するメリット
まず、ステンレス材を冷間鍛造で加工するメリットについて3つに分けてお伝えします。
1つ目は、やはりコストメリットが挙げられます。最小ロット:数千個~という縛りはあるものの、量産加工においては冷間鍛造は非常に効率的であり、一度、金型を作成すれば、繰り返し使用できるため、1個当たりの製造コストは大きく削減できることが期待できます。
当社の場合には、冷間鍛造を素材の粗加工を行う工法として考えているので、冷間鍛造に縛られるのではなく、あくまで全切削と比較して加工コスト・加工効率の点でメリットがあるか否かという点で同工法を採用しています。
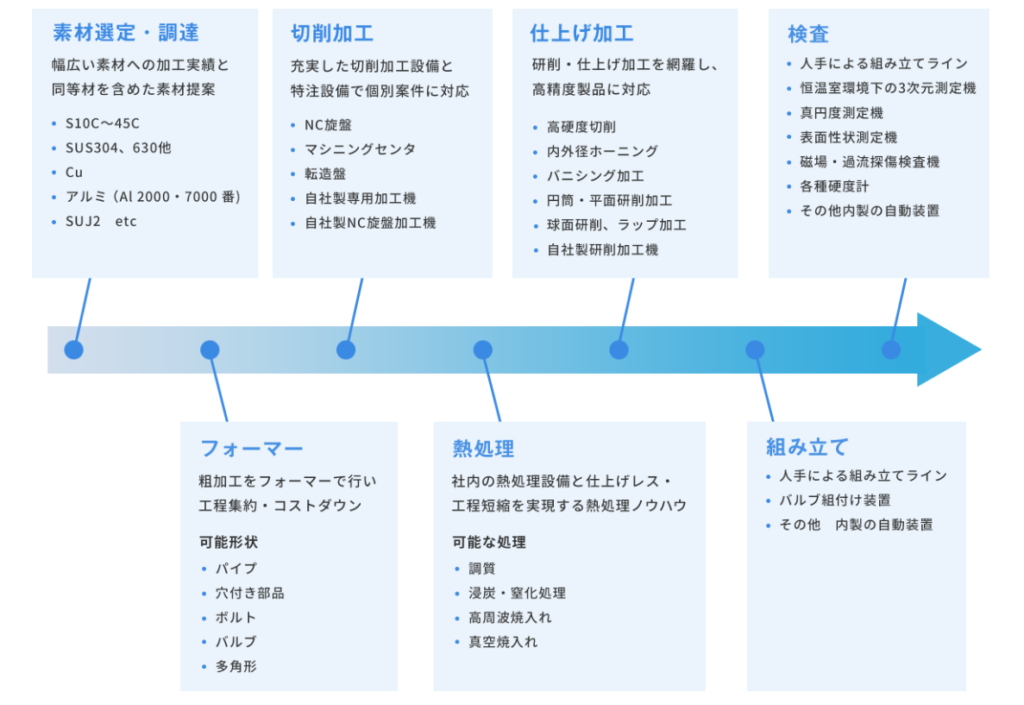
次に、機械特性という点で、ステンレス材に対して冷間鍛造を用いた成形を行うと得られるメリットが高硬度化が挙げられます。もともと、硬度が高いとされているステンレス素材ですが、冷間鍛造によって金属の結晶粒が細かくなり、組織が密になることで強度の増加が期待できます。
3つ目が、寸法精度・表面粗さにおいて高い精度が得られるという点です。冷間鍛造は金型を使用して成形するため、一定値以上の寸法公差については実現が可能です。また、高圧をかけて金型による成形・切断を行うため、表面品質も良好となる場合が多く、求められる精度にも寄りますが、表面処理が不要な場合も多く、装飾的な用途にも適しています。ただし、寸法精度や表面粗さが良好・高い精度が出るというのは、あくまで比較対象が鍛造・鋳造の場合であり、切削加工と比較すると精度・面粗さは十分に高精度であるとは言い難いものです。
その為、切削加工品を冷間鍛造に置き換えた場合、十分な精度が出ないといった場合があります。
一方、当社は、冷間鍛造専業メーカーではなく、冷間鍛造も切削加工もできるトータルでの加工コーディネートが可能な会社として設備を取りそろえ、様々な工法転換提案が可能です。
ステンレス製品を全切削から冷間鍛造化するデメリット
一方で、ステンレス製品の冷間鍛造化にはデメリットが2つ存在します。
1つ目は、加工の難易度が高いという点です。ステンレス鋼は、他の金属に比べて硬度が高く、冷間鍛造の際にひび割れや破損が発生するリスクがあります。このため、加工条件を細かく設定し、適切な金型を使用する必要があり、経験豊富な技術者が求められます。
2つ目は、成形サイズ・形状に制限があるという点です。フープ材という丸材を基に圧力を加え、成形していくため、軸もの形状がほとんどで角を持つ形状は不向きと言えます。さらに、深い凹形状や長さをもつ貫通穴などは非常に難しく、ステンレスを材質として加工を行うとなる極端に難易度が高くなるため、ほかの工法を検討しなければならない場合があります。
一方、当社では他社では難しいとされる加工限界の加工に取り組んでおり、冷間鍛造による、「段付きの軸もの形状」「長穴加工」「プレート形状の加工」などの実績があります。詳しい内容は各ページのでご覧ください。
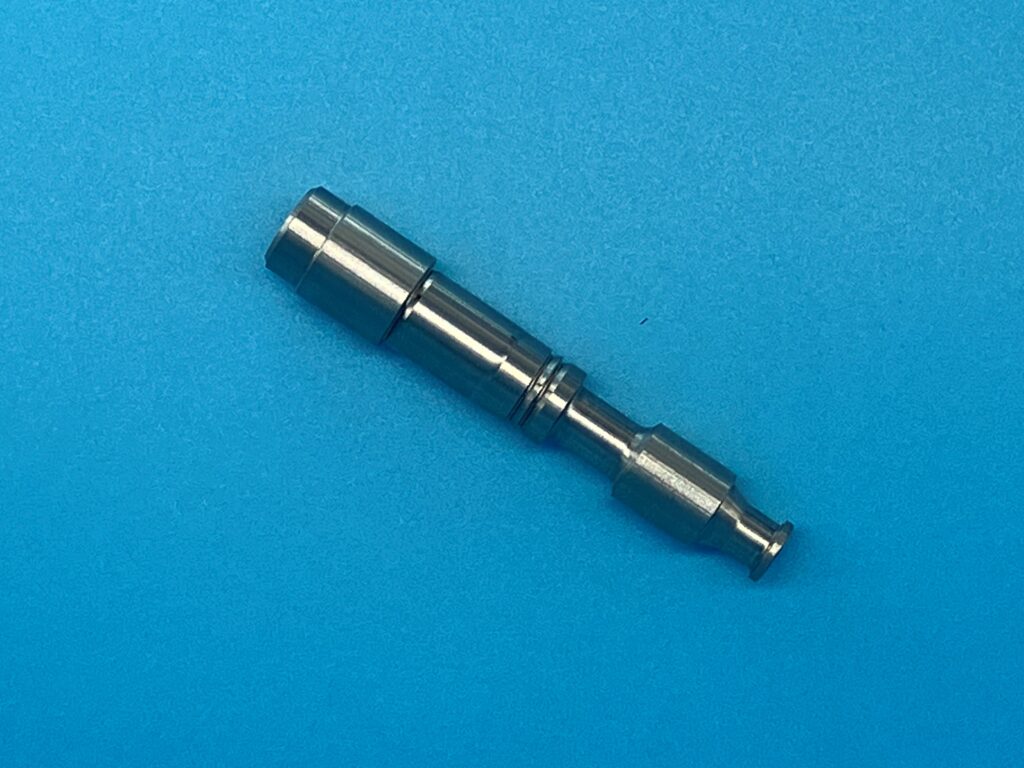
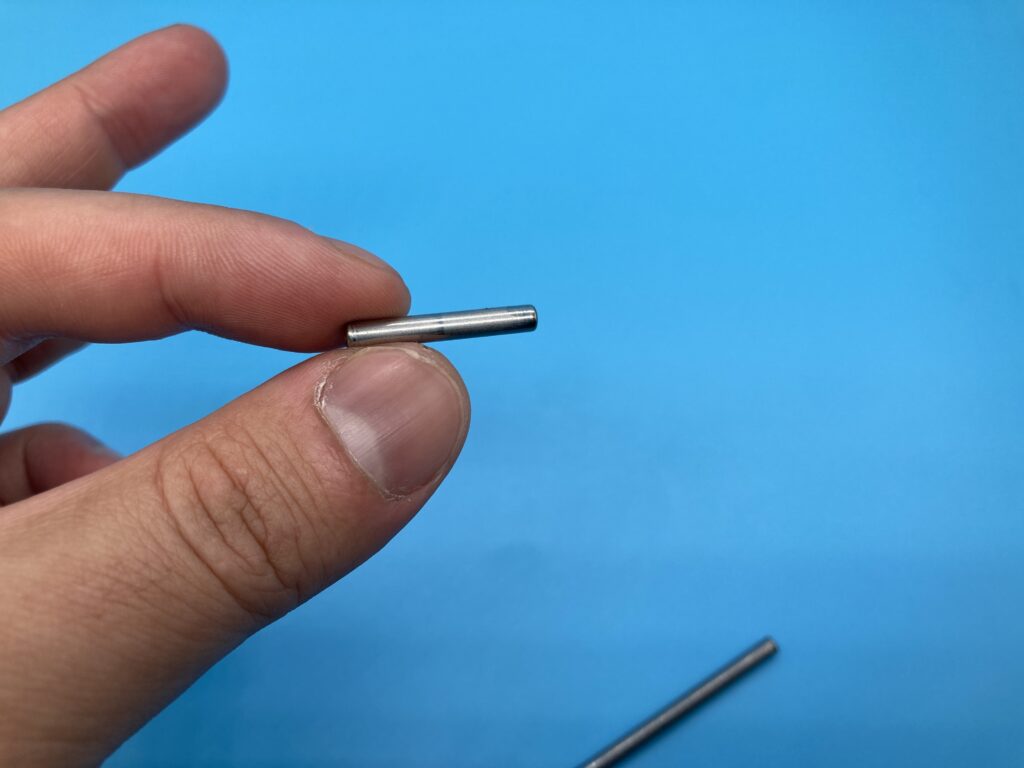
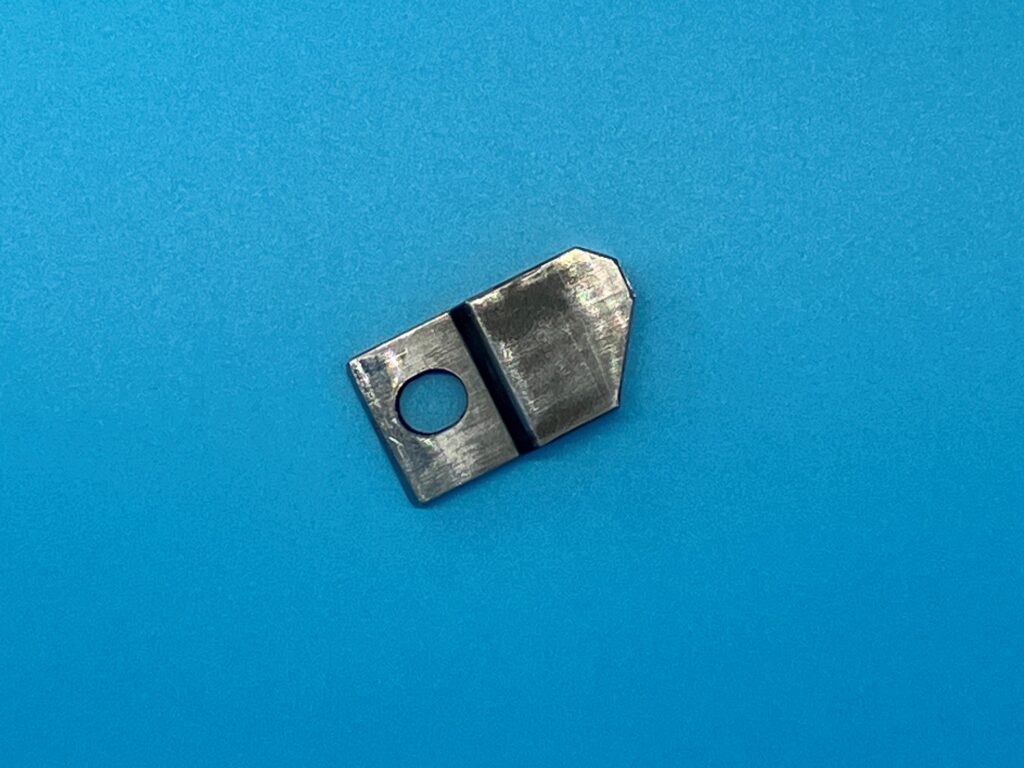
ステンレス製品の冷間鍛造化についてまとめ
ステンレスの冷間鍛造は、その高い強度や優れた寸法精度など、多くのメリットを持つ加工方法です。さまざまな産業で広く利用され、特に高強度が求められる部品や、精密な寸法が必要な部品の製造において重宝されています。
一方で、高難度の加工や設備のコスト、限られた成形能力などのデメリットも伴います。これらの利点と欠点を理解し、適切な用途や条件を選定することで、冷間鍛造の効果を最大限に引き出すことが可能です。冷間鍛造を用いたステンレス製部品は、耐久性と機能性を兼ね備えた材料として、これからも重要な役割を果たし続けるでしょう。
ステンレス製品の冷間鍛造化事例紹介
1.ステンレス製パイプ
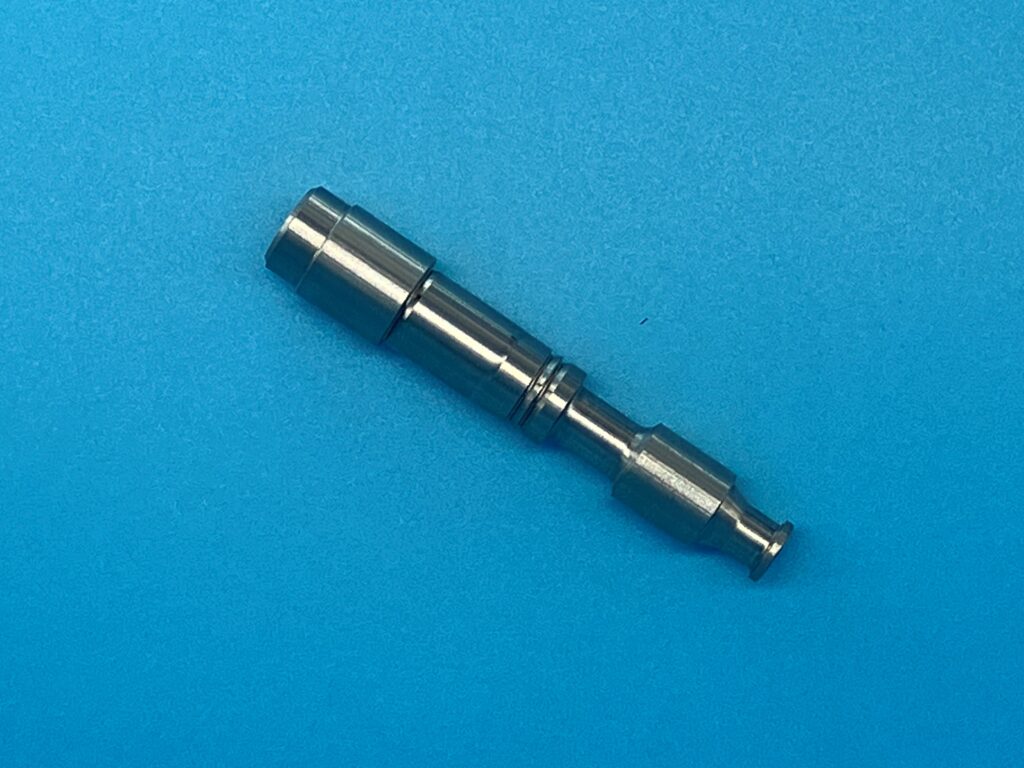
本製品はステンレス製パイプという製品です。形状は写真の通り、複数の段がついている複雑形状を持ち、かつ細かな幾何公差がある製品であったため、当初は切削での加工を検討されていました。ただし、切削となるとコストアップを招くため、代替の工法がないか?とご相談をいただきました。
2.ガス噴射用ステンレスノズル
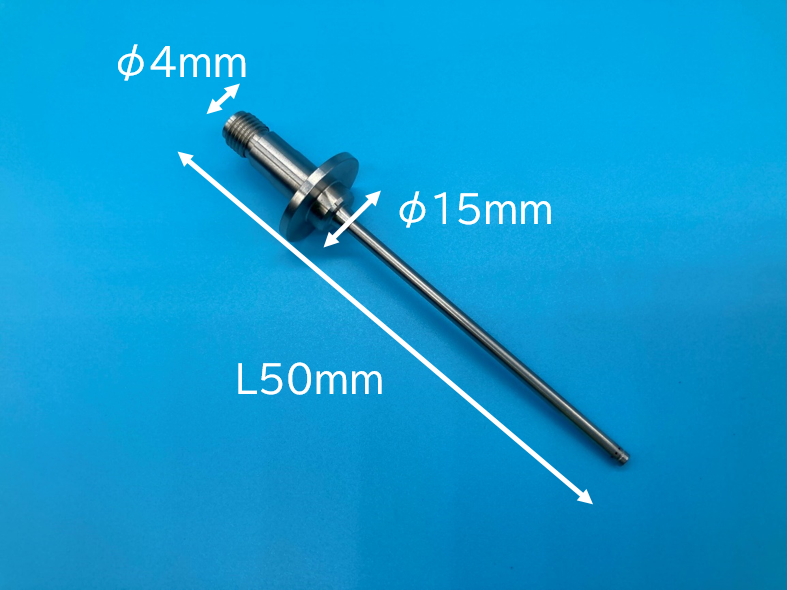
本事例は、量産精密金属加工 コストダウンセンターが加工したガス噴射用ステンレスノズルという部品で医療機器・自動車の内燃機関に使用されたテスト部品です。
加工におけるポイントとして、ノズルのパイプ部分が冷間鍛造+放電加工で加工をしており、切削レスで高い精度を実現しました。
冷間鍛造技術を用いたコストダウン情報を技術ハンドブックとして無料進呈中!
量産精密金属加工 コストダウンセンターでは、冷間鍛造を活用した工法転換によるコストダウン提案、形状変更・図面変更による機能性向上のためのVA・VE提案に力を入れ、自動車系Tier1メーカー様、建設機械メーカー様から高い評価をいただいてきました。
下記では、その技術情報を集約した提案実績を多数掲載しています。詳しくは下記をご覧ください。(画像をクリックいただけましたら、ダウンロードすることが可能です!)
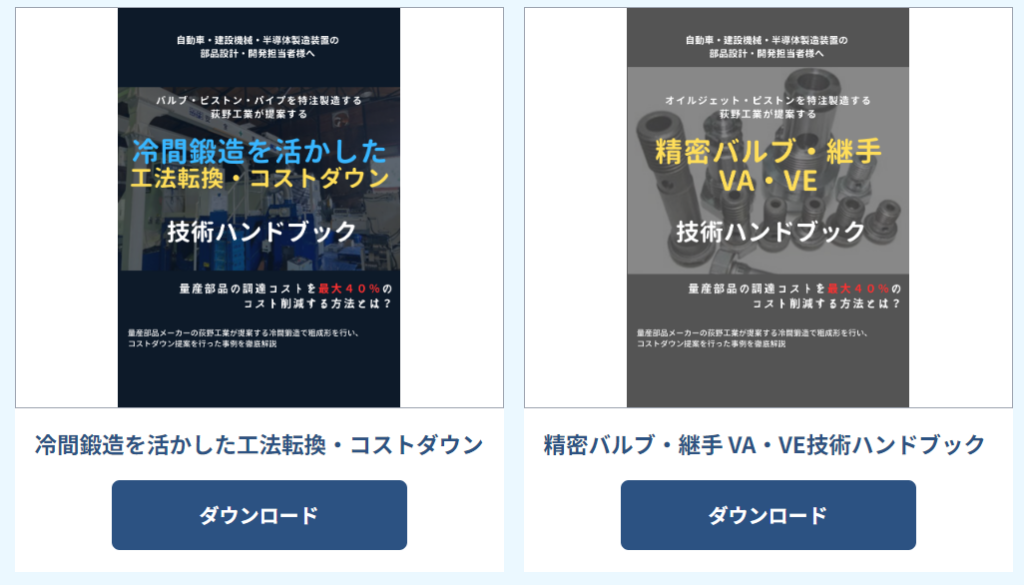